Do You Have A Project We Can Help With?
Specialists In Modern Absorption Chillers
A cost-effective cooling and heating solution that can better utilize existing thermal energy sources
BROAD U.S.A. is a privately held company headquartered in New Jersey, with sales and service operations to support our customers throughout North America. BROAD Absorption Chillers are currently operating successfully in over 80 counties with over 35,000 systems deployed worldwide. Relying on our innovative and environmental-friendly technology, BROAD U.S.A commits itself to optimize energy efficiency for clients in Commercial, Civil and Industrial markets.
Broad U.S.A. has service and support teams in our east and west coast locations, with service engineering and component inventory for rapid service to our customers.
Broad U.S.A. also encourages and supports the education of both operators and service contractors on your equipment by offering regional training courses on a semi-annual basis as well as yearly factory training in our headquarters.
Broad U.S.A. is committed to the inherent value and flexible solutions that thermally driven absorption plays in our modern world. Absorption design is our core competency and primary focus. Unlike many current players in the absorption market, Broad designed and created its first Absorption Chiller in 1988 with its own human capital and innovation, hard work, and the continuous drive to be the best.
Explore Recent Installations
Broad U.S.A. is committed to the inherent value and flexible solutions that thermally driven absorption plays in our modern world.
Our Core Values
Every day, BROAD U.S.A. aims to demonstrate our loyalty to our customers, fairness to our vendors, and dedication to our employees. Long term relationships are more important than gains or losses.
What our clients say about us
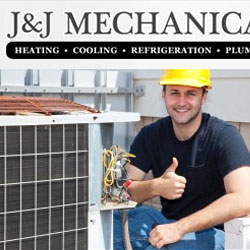
“As a contractor my business model is to reduce risk. For me the economics and benefits of allowing the manufacture to assume this responsibility was the right decision for J&J and my customers.”
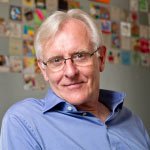
“Broad bid and was the selected as the low cost high quality supplier for this portion of the job”. They performed smoothly and eliminated a lot of coordination issues that would have undoubtedly arisen with out there expertise and familiarity with what is required to join the chiller.
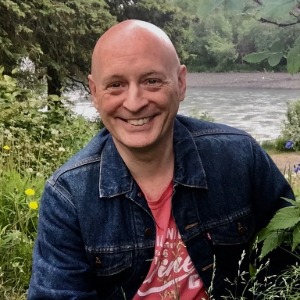
“It is impossible to fulfill great visions and ambitions without developing and sustaining an extraordinary team of talented people along with a underlying culture that binds them together in unity. Such a rare circumstance is evident at BROAD Group.”
Latest News
For Humanity’s Future BROAD’s Unique Building Energy Conservation Technology Protects the Earth BROAD’s Unique Clean Air Technology Protects Mankind.
BROAD U.S.A. Hosts its Annual Customer Appreciation Event at Gansevoort Meatpacking Hotel
Manhattan, New York —— BROAD U.S.A. hosted its Annual Customer Appreciation Event at Gansevoort Meatpacking Hotel on December 12th to celebrate the successful commissioning of its high-efficient maglev chiller BC45, a 150-ton oil free
BROAD Wins the CGCC-Chicago “2022-2023 Cutting-Edge New Energy Innovator Award”
November 20th, 2023, Chicago Illinois --- BROAD U.S.A. proudly announces that we have been honored the “Cutting-Edge New Energy Innovator Award” by the China General Chamber of Commerce U.S.A. – Chicago in recognition of BROAD’s
Holon Building Delegation Visited BROAD Town and Factory
Jeremy Zimman, BROAD U.S.A.’s Director of Communications, led a delegation of architects and developers from across the U.S. to BROAD Town earlier this month to visit our state-of-the-art BROAD Sustainable Building factory, and to experience
Trusted Clients
When the trust account is high, communication is easy, instant, and effective.